How Chip Down Design Optimizes Performance and Reduces Cost
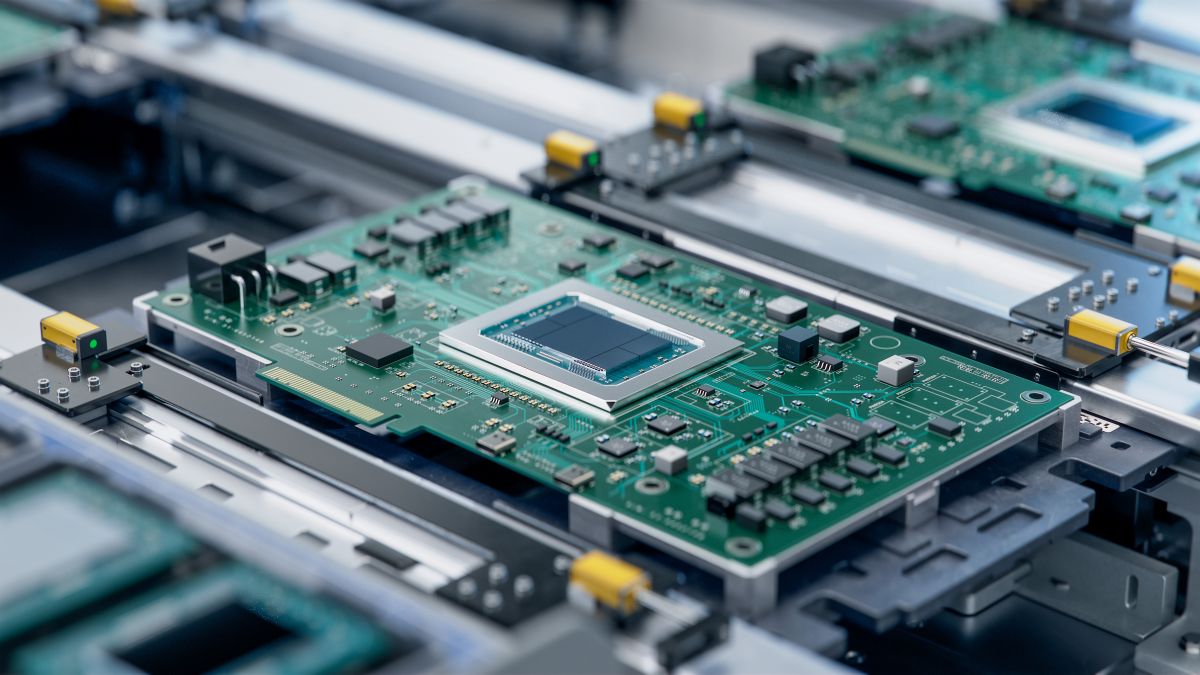
When launching a new product, many companies prioritize speed to market, often leveraging off-the-shelf modules to simplify early development. This approach makes sense as it minimizes risk, accelerates prototyping, and reduces upfront engineering costs. But once a product gains traction and scales, this early convenience can turn into a cost burden.
This is where chip down design becomes a strategic advantage. By transitioning from modular components to a custom chip down solution, companies can optimize performance, reduce bill of materials (BOM) costs, and improve long-term product scalability.
The Turning Point: From MVP to Scale
Most companies enter the market with a Minimum Viable Product (MVP), a functional prototype or early version of their product that is designed for market validation (usually to validate interest or functionality). These early units often use pre-certified modules, development boards, or System on Modules (SoMs) to minimize engineering development effort and regulatory compliance. Use of modules in designs are an entirely valid strategy when either rapid time to market or validation is required, but typically applied to low volume products.
However, as demand grows or the anticipated product volumes justify engineering costs, it becomes clear that off-the shelf modules bring inefficiencies:
- Higher BOM Costs: Pre-built modules may simplify development, but they include extra, often unnecessary components that drive up per-unit costs
- Performance Limitations: Generic modules are designed for broad use cases, meaning they may not be fully optimized for the specific needs of your product
- Scalability Issues: As production ramps up, relying on a third-party module supplier adds risk to availability, pricing, and supply chain control
Once a product has proven market fit, investing in a chip down redesign eliminates these limitations while unlocking major cost savings.
How Chip Down Design Lowers Costs and Enhances Performance
1. Eliminating Unnecessary Components
Pre-built modules include a variety of extra features to accommodate multiple applications, but your product likely only needs some of these functions. By moving to a custom chip down design, you can remove unnecessary hardware, simplifying your PCB and reducing BOM costs.
2. Direct Sourcing of Components
When using a module, you’re paying a markup for the convenience of integration. By designing the chip directly onto the PCB, you gain direct control over component sourcing, reducing supplier dependence and allowing cost-optimized purchasing.
3. Power and Thermal Optimization
Modules often include power regulation and signal conditioning circuits designed for broad compatibility, leading to inefficiencies in power consumption and heat dissipation. A chip down approach optimizes power delivery, improving efficiency and battery life, which is particularly important in consumer electronics and medtech.
4. Customization for Performance Gains
A chip down design enables tighter integration with board-level components, leading to better signal integrity, improved processing efficiency, and optimized RF performance, especially with custom-tuned antennas. By eliminating unnecessary I/Os and features, this approach reduces overhead while ensuring equal or superior performance. Additionally, it streamlines firmware packaging, making the device more efficient and responsive.
5. Long-Term Supply Chain Control
With a chip down approach, you’re no longer locked into a single module vendor. You gain the ability to manage supply chain risks, negotiate better pricing, and ensure continuity of supply, which is critical as your product scales into higher production volumes. In addition, should you require a change in architecture to meet different requirements, you are at liberty to do so.
If your product is scaling successfully and product volumes justify the engineering investment, it’s time to assess a chip down redesign. At Pegmatis, we specialize in helping companies navigate the decision and development to transition from modular prototypes to high-performance, cost-optimized chip down solutions. Our engineering team brings deep expertise in hardware, firmware, and software, ensuring a seamless migration that reduces risk while unlocking performance and cost benefits. If you are ready to explore the advantages of chip down design, get in touch with our team today.
Your trusted product development partner
Pegmatis is your ultimate end-to-end design partner, delivering exceptional hardware, software, and firmware solutions to bring your product vision to life. We specialize in high-fidelity design, cost-driven architecture, and seamless manufacturing support, leveraging our extensive network for mass production. Whether you need expertise with medical products, regulated industry solutions, connected technology, or other complex innovations, our team is equipped to handle even the most complex challenges.
Our story began as an elite design center for a Fortune 500 company, where we collaborated with top-tier customers to launch numerous high-volume products into the market. In 2016, Pegmatis emerged as an independent entity, carrying forward the same Dream Team and adding an elite software group to provide truly comprehensive product development services. With Pegmatis, you're not just hiring experts; you're partnering with a proven team dedicated to your success.
Related Blogs
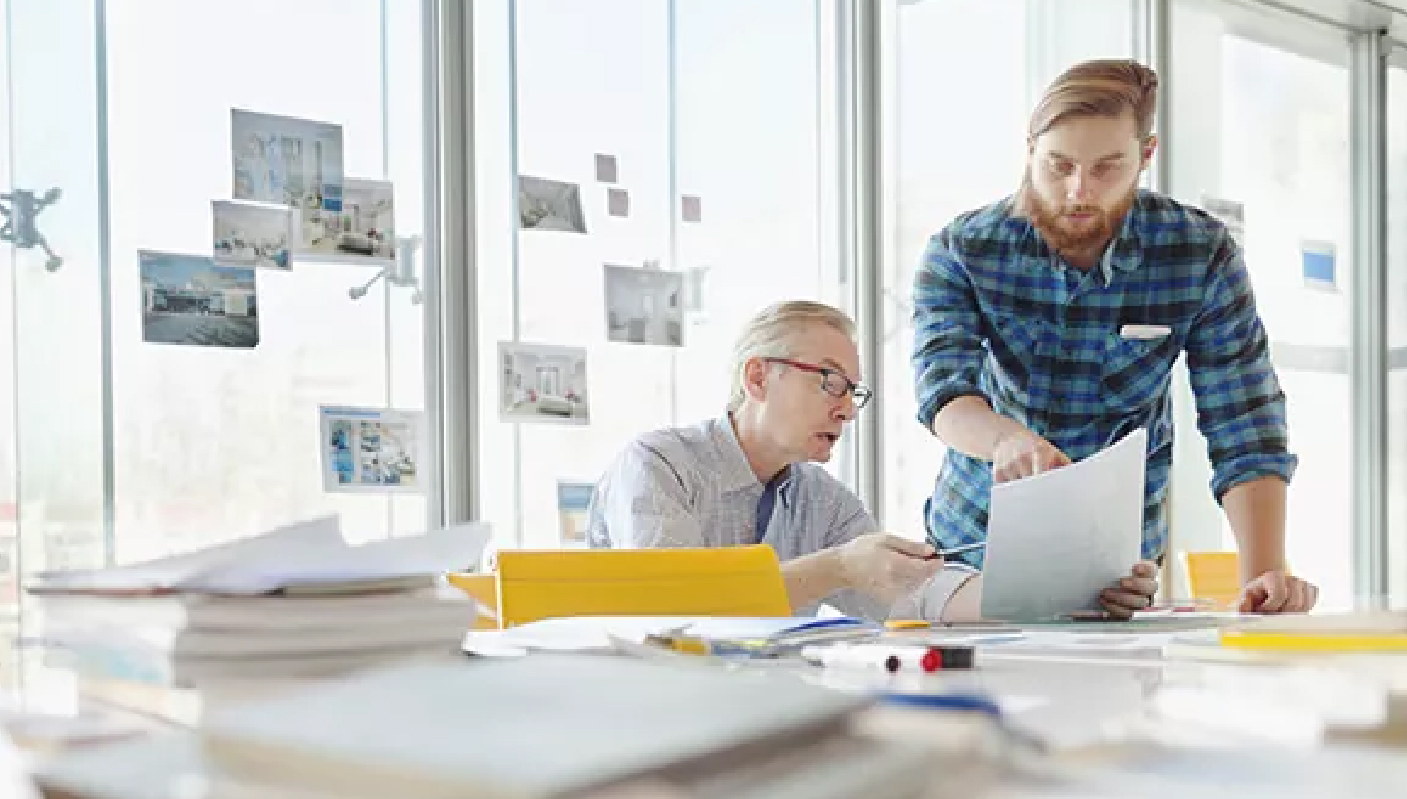
Product Requirements: Do You Know What You Need?
This month, I give the writing reins to my partner and co-founder of Pegmatis, Ronald Cassar, BA(Hons).
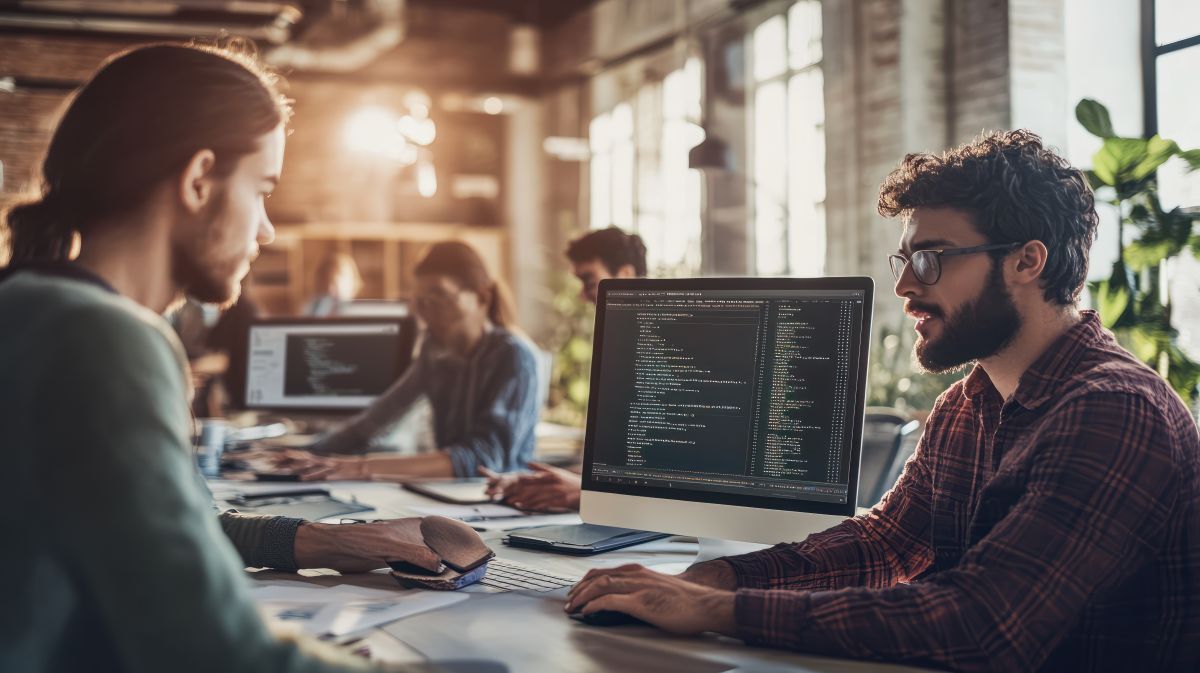
Our Firmware Development Process
The Pegmatis firmware development process is structured in to address client goals, minimize downtime, and maximize efficiency.
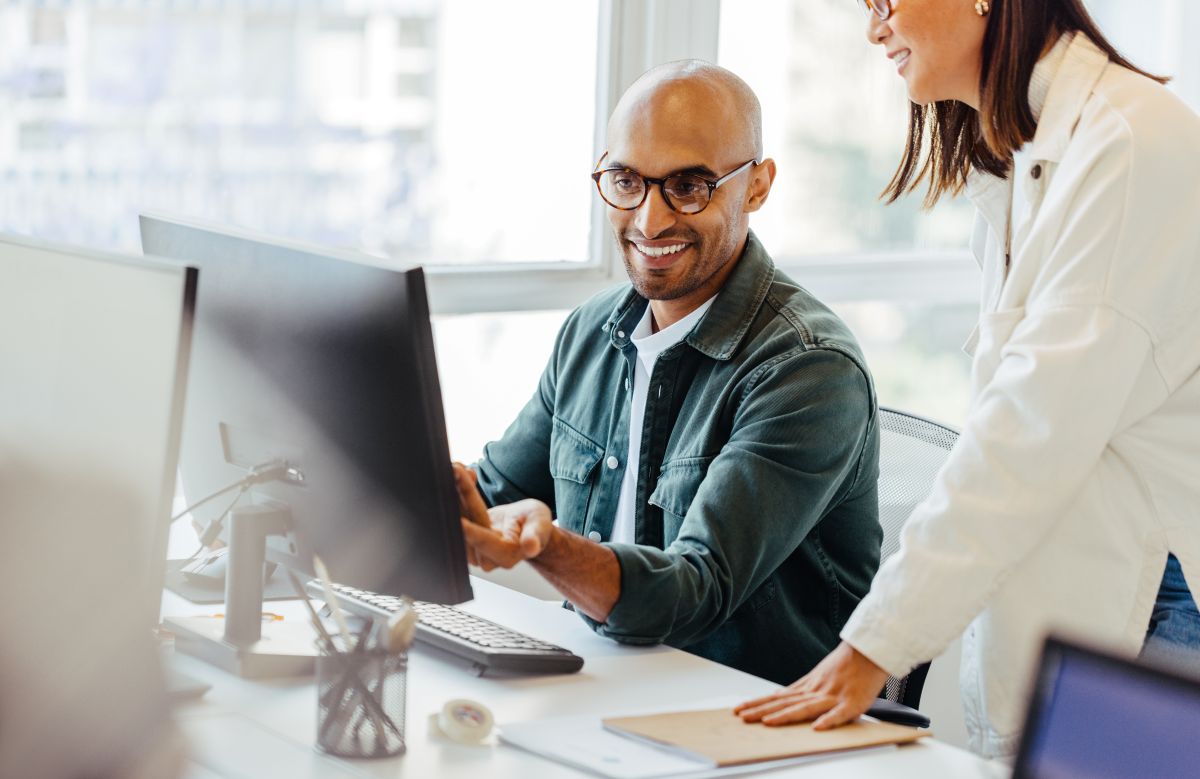
A Guide to the Medical Device Development Process
Whether you’re launching a new product or refining an existing device, understanding the medical device development process is essential to ensure compliance, quality, and market success.